SCR Catalyst: Reducing NOx Emissions for Cleaner Air
Understanding SCR Catalysts: A Key to Cleaner Air
In the quest for cleaner air and a healthier environment, industries grapple with the challenge of mitigating harmful emissions. Among these, nitrogen oxides (NOx) pose a significant threat, contributing to smog, acid rain, and respiratory problems. Fortunately, innovative technologies like Selective Catalytic Reduction (SCR) offer a powerful solution. At the heart of this process lies the SCR catalyst, a crucial component that facilitates the conversion of NOx into harmless nitrogen and water vapor.
The Magic Behind SCR Catalysts
SCR catalysts are the unsung heroes of NOx reduction. These intricate structures, often composed of ceramic materials like titanium oxide, are infused with active catalytic components such as base metal oxides (vanadium, molybdenum) or precious metals. Their porous design provides a large surface area where the magic happens: NOx molecules in the exhaust gas react with a reductant, typically ammonia or urea, in the presence of the catalyst. This reaction transforms NOx into harmless nitrogen and water, effectively cleaning the exhaust gas before it’s released into the atmosphere.
The specific reactions involved depend on the reductant used:
With ammonia: 4NO + 4NH3 + O2 → 4N2 + 6H2O
With urea: 2NOx + (NH2)2CO + ½ O2 → 2N2 + CO2 + H2O
These reactions occur within a specific temperature window, typically between 357 and 447 °C, although lower temperatures can be effective with longer residence times.
Choosing the Right SCR Catalyst
SCR catalysts come in various forms, each with its own strengths and weaknesses, making the selection process crucial for optimal performance.
Honeycomb Catalysts
Honeycomb catalysts, resembling a honeycomb structure, are the most common type. Their advantages include:
High surface area: This allows for greater contact between the exhaust gas and the catalyst, promoting efficient NOx reduction.
Good mixing: The honeycomb structure facilitates turbulence, ensuring thorough mixing of the exhaust gas and reductant.
However, they are also prone to:
Clogging: Fly ash and other particulate matter can accumulate in the channels, reducing efficiency and increasing pressure drop.
Higher pressure drop: The intricate channels can restrict gas flow, requiring more energy to push the exhaust through the system.
Explore Our Range of High-Performance Honeycomb SCR Catalysts
Plate Catalysts
Plate catalysts consist of flat, parallel plates coated with the catalyst material. Their benefits include:
Lower pressure drop: The open structure allows for easier gas flow, reducing energy consumption.
Less prone to clogging: The flat surfaces are less likely to trap particulate matter.
However, they have drawbacks such as:
Lower surface area: Compared to honeycomb catalysts, they offer less contact area for the reaction, potentially reducing efficiency.
Larger size: Plate catalysts require more space, which can be a constraint in some applications.
Corrugated Catalysts
Corrugated catalysts offer a balance between honeycomb and plate types, with a wavy structure that provides a higher surface area than plate catalysts while maintaining a lower pressure drop than honeycomb catalysts. However, they are less common and may have a higher cost.
The Role of Reductants in SCR
The effectiveness of SCR technology also relies on the choice of reductant, each with its own safety and handling considerations.
Anhydrous ammonia: Highly efficient and widely used in large industrial applications. However, it is a hazardous gas requiring strict safety protocols for storage and handling.
Aqueous ammonia: A safer alternative to anhydrous ammonia, easier to store and transport. However, it requires vaporization before injection into the SCR system.
Urea: The safest option, commonly used in automotive applications. It requires thermal decomposition to convert into ammonia before reacting with NOx. However, this process adds complexity to the system.
SCR Catalysts in Action: Applications Across Industries
SCR technology with its diverse catalyst options and reductants finds widespread application in various industries grappling with NOx emissions.
Power plants: SCR systems are essential for reducing NOx emissions from coal, oil, and gas-fired power plants. They are typically installed between the economizer and air preheater, with ammonia or urea injected upstream of the catalyst.
Heavy-duty vehicles: SCR catalysts are crucial for meeting stringent emission standards for diesel engines in trucks, buses, and other heavy-duty vehicles. Urea is the preferred reductant due to its safety and ease of storage.
Marine engines: SCR systems help reduce NOx emissions from ships, contributing to cleaner air in ports and coastal areas.
Industrial boilers and furnaces: SCR technology is used in various industrial processes, such as cement production, waste incineration, and chemical manufacturing, to control NOx emissions.
Challenges and Solutions in SCR Technology
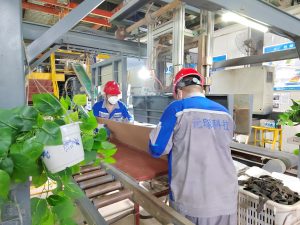
scr catalyst production workshop.
Despite its effectiveness, SCR technology faces challenges that require careful consideration and mitigation strategies.
Catalyst poisoning: Sulfur compounds, heavy metals, and other contaminants can deactivate the catalyst, reducing its efficiency and lifespan. Proper fuel selection, fuel cleaning, and the use of upstream scrubbers can help prevent poisoning.
Catalyst plugging: Fly ash and particulate matter can accumulate in the catalyst, especially in honeycomb types, leading to increased pressure drop and reduced performance. Regular cleaning with sootblowers or ultrasonic horns is necessary.
Ammonia slip: Unreacted ammonia passing through the SCR system can contribute to emissions and form ammonium salts that can damage downstream equipment. Optimizing the ammonia injection and ensuring proper mixing can minimize slip.
Cost: Implementing and maintaining SCR systems can be expensive, requiring careful cost-benefit analysis.
SCR catalysts are at the forefront of the fight for cleaner air. By understanding their function, types, and applications, industries can harness the power of this technology to minimize their environmental footprint and contribute to a healthier planet.